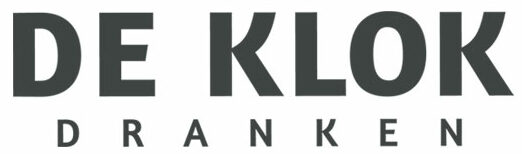
Behind a well-tapped beer at your favorite pub or a surprisingly delicious wine at your favorite restaurant, there is an entire logistical operation. De Klok Dranken is the wholesaler that supplies catering establishments throughout the country with all their beverage needs in a timely manner. The organization has recently started using SAP Extended Warehouse Management to organize their distribution centers.
Harry Smits, Manager of Hospitality Operations at De Klok Dranken, and Gerard Mul, IT Business Partner at De Klok’s parent company Grolsch, talk about how, together with Quinso, they made the move from paper to digital processes.
De Klok Dranken is a wholesaler of beverages, food and non-food items for the hospitality industry. Grolsch’s independent subsidiary supplies a wide range of beers and beverages, and advises hospitality partners on products, trends and developments. De Klok has five distribution centers. From these warehouses, they supply customers all over the country. From the café on the corner to the biggest events in the Netherlands, the most famous of which is “De Zwarte Cross”.
Harry Smits is responsible for distribution and customer service for De Klok Dranken. He explains why the organization decided to digitize its distribution processes: “We use to do everything on paper, but then we grew significantly in just a couple of years. Our volumes increased, our assortment expanded and we got more and more customers.”
Looking for more insights and efficiency
Strong growth often puts pressure on analog warehouse processes. It creates long picking lists and a worse overview regarding our stock position. It is also difficult to involve temporary workers to scale up during busy times, as they must first be trained extensively to make the process their own. Smits confirms this: “Due to the growth of the company, it was unsustainable to continue like this. We had to digitalize.”
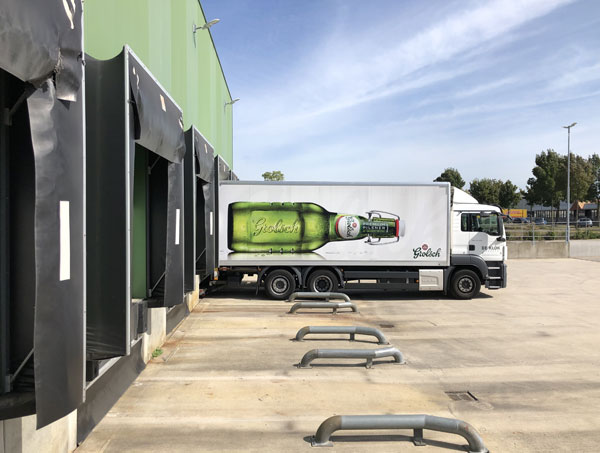
SAP Extended Warehouse Management (EWM).
For the right solution, Smits did not have to look long. Indeed, parent company Grolsch has been using SAP EWM, a solution that makes it easier to manage high-volume warehouse operations, since 2015. SAP EWM integrates complex supply chain logistics with warehouse and distribution processes. It provides users with transparency and control, optimizing real-time inventory tracking.
Gerard Mul is responsible for manufacturing, supply chain and logistics at Grolsch. He explains why he also recommended the solution to subsidiary De Klok Dranken: “We have good experiences with SAP EWM. The solution provides efficiency gains in our distribution centers. That’s why we advised De Klok Dranken to implement the same system.” Smits was quickly convinced. “De Klok has been operating on an SAP infrastructure since 2000. We were convinced that EWM would fit in well with our existing IT environment.”
Premium company, premium partners
De Klok Dranken chose to be guided by Quinso during the digitization process. Together with Quinso, De Klok, EWM rolled out at the five warehouses. Smits explains why they engaged Quinso: “The transition to SAP EWM was a big change for us. We wanted our people on the shop floor to be as prepared as possible for the transition and to know what to expect. That’s why we chose to tackle the implementation and change process thoroughly with a professional partner.”
“With Quinso, we just clicked,” says Smits. “They took us through the processes and were on the same line as us. During the process, the consultants also proved to be involved and enthusiastic.” Mul also remembers why Quinso came out on top of the tender process: “Quinso came across as a proactive party. The same people who eventually did the work already showed up during the pre-sales phase. So they knew exactly what we wanted. That doesn’t happen often! As a premium company, Grolsch wants to work with premium partners. Quinso is such a partner.”
Building on proven successes
During the digitization process, Quinso set up as many of De Klok’s work processes as possible according to proven best practice standards for retail. This meant that only 20 percent of the processes had to be adapted for The De Klok specific processes. Following best practices ensured a short implementation time and made it easy for De Klok to quickly take follow-up steps with EWM.
The best practices were a great solution for De Klok Dranken. Mul: “Our warehouse processes are quite common. Therefore, we were able to use existing standards. Moreover, we wanted to move towards one common way of working at the five locations. That’s where the standards offered a lot of guidance.”
De Klok also found this foothold in the step-by-step method of implementation: “We implemented SAP EWM per branch. This had the advantage that we could take lessons from the implementations at the other branches.”
Trained within half an hour
Now that SAP EWM is running at all of De Klok Dranken ‘s warehouses, Harry Smits looks back on a successful digitization project: “We wanted to improve our inventory and delivery reliability and gain more insight into our processes. In order to ultimately increase efficiency in our warehouses. We succeeded.”
Gerard Mul explains what this new reality entails: “We can now use flex workers who are trained within half an hour to use voice picking to prepare orders for delivery to our customers. People no longer walk through the warehouse with paper pick lists, but with headsets and scanners. A completely paperless warehouse with complete digital order picking process. That’s thanks in part to the hard work of Quinso. They have been able to make our ambitions come true.”