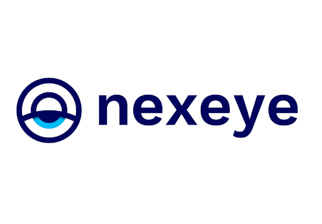
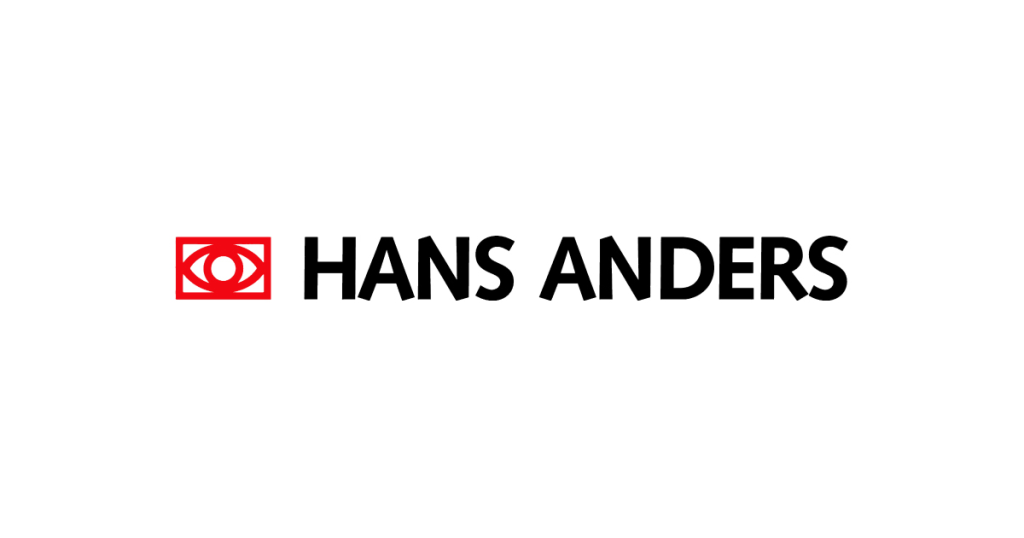
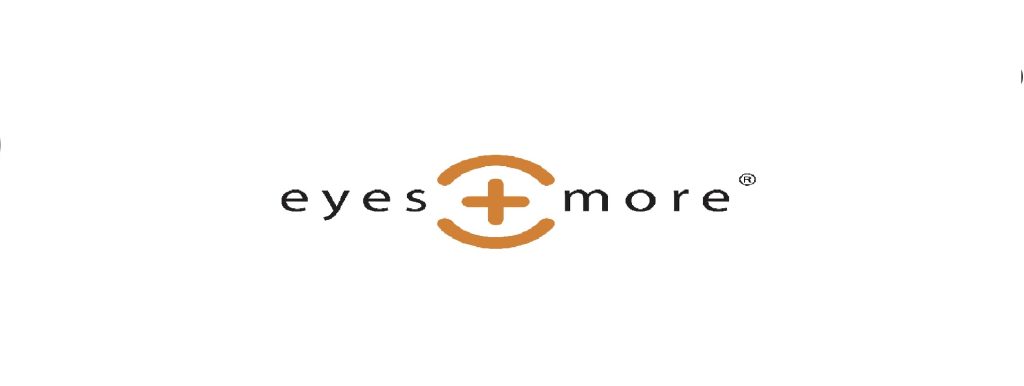
How do you keep high-quality eye and hearing care accessible and affordable for everyone? This ambitious mission has optics chain nexeye, which includes the brands Hans Anders, Direkt Optik and eyes + more. Add to this mission a substantial growth from 450 to over 730 stores in a few years, and you know that consistent digitization of processes in all areas is a key requirement. Nexeye built on its existing SAP system with ORBIS Logistics. In this, Quinso was responsible for the technical implementation in the central warehouse in Gorinchem.
From nexeye, Sanne Oosterhoff, COO, and Pieter van de Veer, interim project manager, talk about how they made the transition from paper to digital processes with Quinso. Rogier Leijsen, project manager at Quinso, explains what the challenges were during this project.
Digitization as a necessary step forward
Nexeye is a European leader in optical retailing, which currently consists of three low-cost optical brands. And operates in five European countries – Germany, the Netherlands, Belgium, Austria and Sweden. All brands combined have 734 stores and more than 4,000 employees.
The brands are managed by the global Shared Service Center with warehouse in Gorinchem. From there, eyewear, contact lenses and lenscare products, hearing aids and hearing protection are supplied to all stores and directly to consumers. Nexeye is best-in-class in omnichannel retail within the optical industry, thanks to far-reaching investments in digitalization and innovation.
From paper to digital: the transformation to efficiency
Sanne Oosterhoff is ultimately responsible for logistics at nexeye as COO. He explains why the organization decided to move to warehouse digitization: “Nexeye has grown from 450 to more than 730 stores in a few years. To make this growth possible, we have taken measures to supply all brands’ stores even more flexibly, efficiently and sustainably in the future. We have gone from paper to digitally driven work, with multi order picking for the stores and the introduction of tablets and scanners in our warehouse. Digitizing our work processes allows us to work more accurately and efficiently throughout the chain. In addition, we can increase the service level to our labels, stores and customers.”
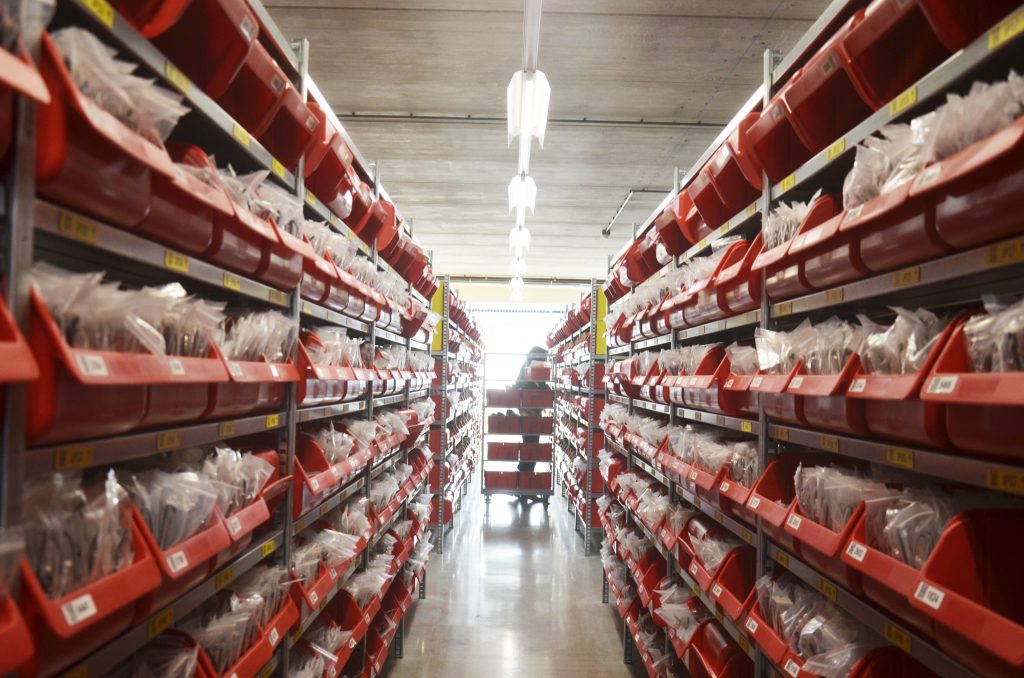
Seamless integration on existing SAP system
ORBIS Logistics is an application that ensures the optimal use of goods movement within the warehouse. Pieter van de Veer explains why nexeye chose ORBIS Logistics has chosen: “ORBIS Logistics connects seamlessly with the existing SAP system used in the warehouse. Nexeye is digitizing its processes with Quinso. Specifically for nexeye, Quinso made a number of adjustments throughout the process. For example, when receiving goods, a number of fields are already filled in automatically, ensuring an efficient start of the process. In addition, when picking frames, a number of additional checks have been built in that help reduce error rates to a minimum. The best improvement is mainly on the outbound side. When placing the frames in the shipping crates, a registration system has been implemented about the number of crates going to a store. This has greatly increased inventory accuracy.”
Productivity increase of 10%
The biggest challenge during the process was getting the people on the floor on board. Getting people excited that digitization actually makes work easier and more efficient. Nexeye included end users in the process and decision making from the beginning. In addition, there has been good communication in the go-live and much time has been put into professional training. The job satisfaction of the 20 end users increased tremendously and productivity increased by over 10%.
Optimizing the picking process: a challenging journey
According to Rogier Leijsen, responsible for the technical implementation from Quinso, the biggest challenge was in implementing the optimized picking process. “Pickwaves were set up to determine the optimal route through the warehouse. This was a challenging process because pickers cannot overtake each other, priorities change throughout the day and capacities per crates vary.” By completely reorganizing the warehouse and optimizing routes beforehand, the most was made out of ORBIS Logistics.
Sustainable future
The result of digitization is found mainly in the fact that warehouse capacity and personnel are better utilized. It also saves up to 15,000 kilometers of paper. This contributes directly to sustainability goals. And a foundation has been laid for a lasting relationship between nexeye and Quinso. For example, new plans are ready to use ORBIS Logistics for other product categories and the add-on will also be implemented at eyes + more next year.